CNC Hot Wire Cutters
Turn your ideas into perfectly cut reality with ThermoCut Pro, the ultimate solution for precision cutting. Designed for professionals who demand accuracy and efficiency, it effortlessly shapes complex 3D objects from materials with densities up to 60 kg/m³.
From polystyrene and styrodur to EPS foams, ThermoCut Pro handles them all with clean, smooth edges and unmatched speed. Whether you’re building, designing, or crafting, this machine transforms your workflow, saving time, reducing waste, and delivering results that impress every time.
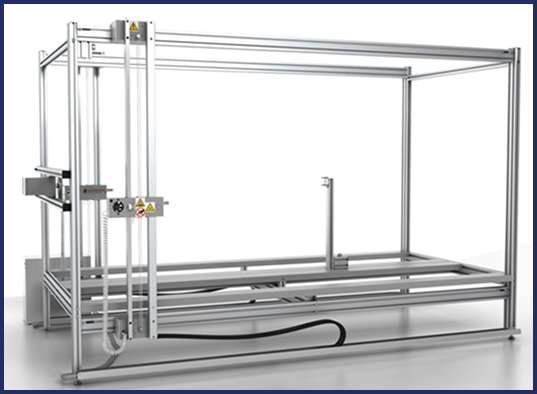
Features
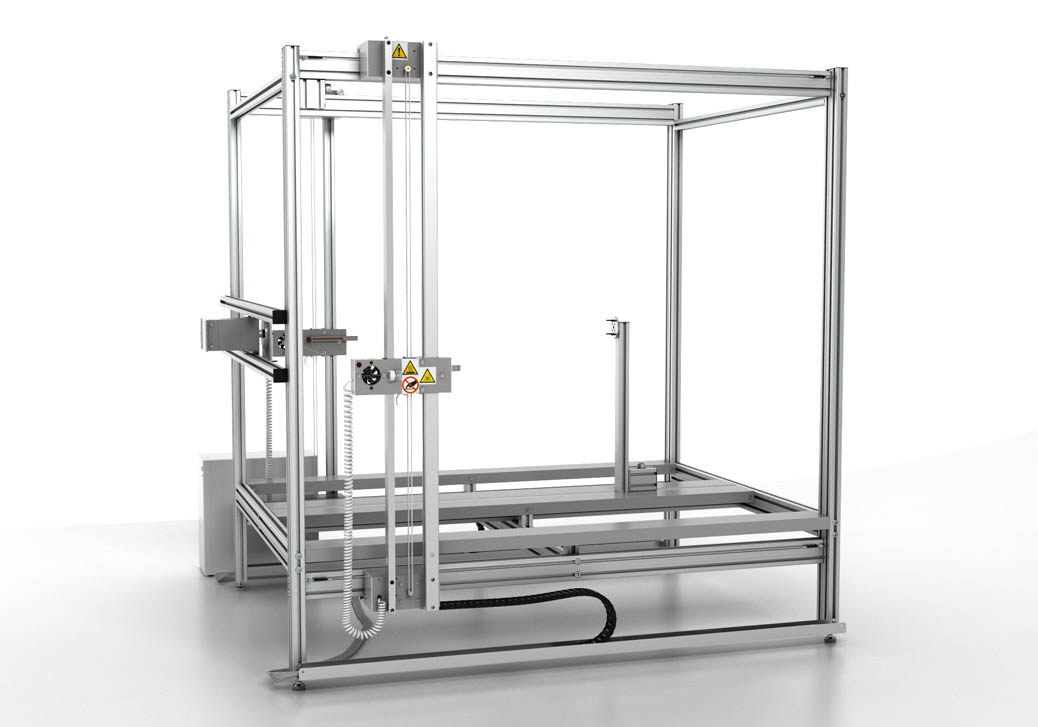
High-Precision Cutting
Delivers accurate cuts with minimal material waste.
User-Friendly Control
Easy-to-use interface for quick setup and operation.
Durable Build
Strong construction for long-lasting performance.
Independent Access Control
Allows separate operation of machine sections for safer, more efficient workflow.
Capable Wire System
Delivers consistent heating for smooth, accurate cuts across varying foam densities.
Material Versatility
Compatible with multiple materials and applications.
Fast Operation
High-speed cutting without sacrificing quality.
Low Maintenance
Simple upkeep with minimal downtime.
Turn Table for Lathe
Enables precise 360° rotation for cylindrical and complex foam cutting.
Available Models
Model | Pro 35 | Pro 60 | Pro 120/150 | Pro 240 | Pro 300 |
---|---|---|---|---|---|
X Workspace (Length) | 130 cm | MINI 130 cm MIDI 240 cm MAX 300 cm |
MINI 130 cm MIDI 240 cm MAX 300 cm |
MINI 130 cm MIDI 240 cm MAX 300 cm |
MINI 130 cm MIDI 240 cm MAX 300 cm |
Y Workspace (Height) | 60 cm | 130 cm | 130 cm | 130 cm | 130 cm |
Cutting Wire Length | 35 cm | 60 cm | 130/150 cm | 240 cm | 300 cm |
Resistant Wire Diameter | 0.25 mm | 0.35 mm | |||
Forming Wire Diameter | 0.9 mm | ||||
Resolution | 0.01 mm | ||||
Max. Shift Speed | 2000 mm/min | ||||
Max. Working Speed | 2000 mm/min | ||||
Resistant Wire Cooling | 2 Cooling Fans | ||||
Number of Stepping Motors | 3 | 6+1 | |||
Cutter Construction | Reinforced Aluminum Profiles | ||||
Power Supply | 220V/50Hz 110V/60Hz | ||||
Power Consumption | 150 W | 200 W | 250 W | 750 W | 950 W |
Interface | Port USB | ||||
Forming Wire | Option | Standard | Option | ||
Revolving Table | Option - S10 | Standard - S150 | Option - S150 | ||
Lathe | Option | Standard | Option | ||
Independent Arm Motion "Perspective" | Unavailable | Standard | |||
Additional Cutting Wires | Unavailable | Option |
Applications
Advertising & Signage
- Large/wide-format outdoor displays
- Decorative letters and trademarks
- Trade graphics and logos
- Trade-post stands
Architecture & Scenic Design
- Entrances, portals, colonnades
- Cornices, keystones, columns
- Decorative interiors
- Film/theatre scenography
Other Uses
- Casting molds and packaging prototypes
- Furniture parts
- Pipe coverings
- Acoustic screens
- General design and modeling
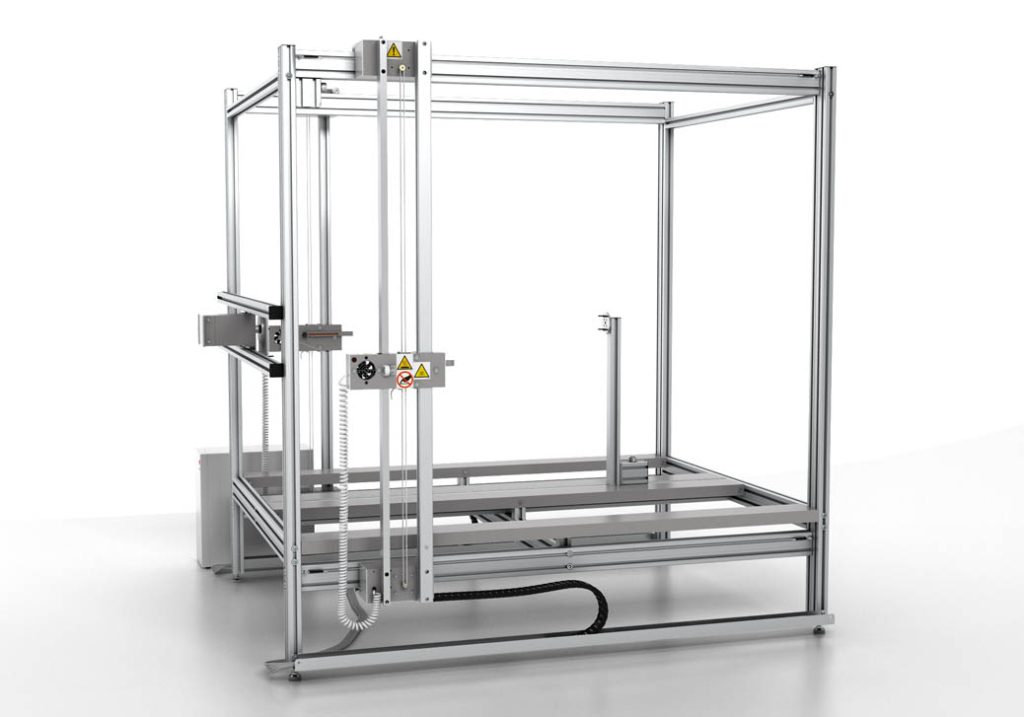
Request Your Quote Now!
customized machinery for a wide range of industries. Feel
free to reach out for any queries. We’d be happy to help!
Call us
+971-50-9942579
Office Address
KASHIF SAEED GENERAL TRADING LLC,
P.O BOX 238071, DUBAI, UAE